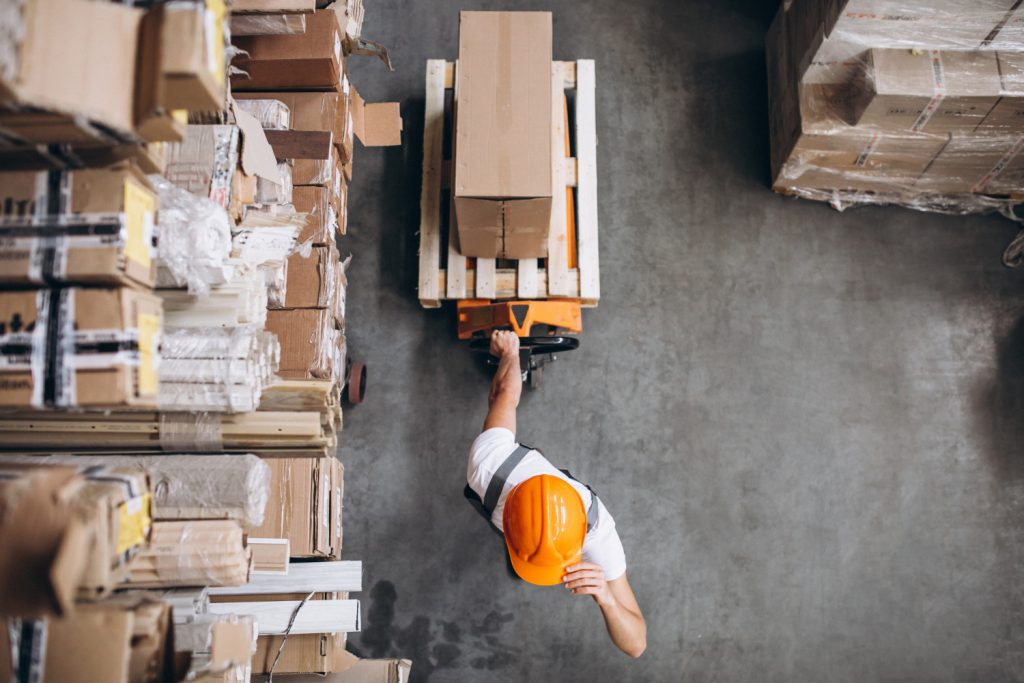
It can be challenging to improve a warehouse’s bottom line, especially for fast-paced businesses such as e-commerce and retail. For one, doing so will likely need substantial upfront costs, which not all businesses are able to shoulder. Similarly, adjustments such as conducting training and optimising warehouse layouts may cause downtime if improperly managed, leading to decreased productivity.
Despite these difficulties, however, improving your warehouse’s bottom line is a must as it directly impacts profitability, operational efficiency, and sustainability. So, to accomplish this objective and help your warehouse stay competitive, you have to come up with strategies that will allow you to overcome existing challenges in the most cost-effective manner.
With that said, here are some effective strategies that you can employ to help your warehouse reduce costs, optimise resources, and improve productivity.
1. Acquire Forklifts for Improved Productivity
Efficient material handling is key to systematic warehouse operations. Forklifts play a huge role in this, allowing operators to navigate the warehouse faster and load more goods to be transported in fewer trips. If your business isn’t in the position to buy a forklift at the moment, then forklifts for rent are a viable solution and can sometimes even be the more cost-effective option.
Adding a forklift (or several ones) to your warehouse fleet allows for increased material handling speed, reduced manual labor, and enhanced safety. Forklifts also let workers move heavy or bulky items quickly, reducing the time spent on loading, unloading, and stacking inventory. By streamlining warehouse tasks, forklifts are able to increase productivity while reducing operational costs in the process.
2. Optimise Inventory Management
Proper inventory management helps reduce unnecessary costs while ensuring that products are available when you need them. In this vein, another effective strategy would be to implement demand forecasting or just-in-time (JIT) inventory, meaning that goods are only ordered and received as they are needed. This setup allows you to minimise overstocks that can lead to high holding costs or stockouts that result in lost sales and dissatisfied customers.
You can also improve inventory placement by reviewing which of your goods have high demand, and then make sure they’re stored in the most accessible locations for quick handling. In addition, consider adopting a warehouse management system (WMS) to track stock levels in real-time, thus improving inventory accuracy and reducing human errors.
3. Enhance Warehouse Layout and Space Utilisation
A well-organised warehouse layout can significantly improve efficiency as it reduces travel time for workers and maximises storage capacity. You can start by placing frequently picked items closer to packing stations, which minimises the movement needed to fetch them and thus speeds up order fulfillment. Also, make sure there are clearly defined pathways for material handling equipment to reduce congestion and safety hazards.
Another tip would be to utilise vertical storage solutions. Tall racks and mezzanines, for example, maximise vertical space utilisation, allowing more inventory to be stored without needing to expand the warehouse footprint.
4. Provide Worker Training and Incentives
A motivated and well-trained workforce is essential to improving your warehouse’s bottom line. In line with this, make sure to hold regular training programs on safety, equipment handling, and technology use as these can go a long way in improving worker competence. To increase workforce flexibility, you may also train workers for multiple adjacent roles to ensure seamless operations even during peak periods.
If your business finances allow it, consider providing performance-based incentives as well. Offering bonuses or rewards for efficiency and accuracy encourages employees to be more efficient. It also contributes towards creating a more positive work environment.
5. Invest in Warehouse Automation and Technology
Adopting technology enhances accuracy, speed, and overall productivity in your warehouse while also reducing labour costs. A simple barcode or RFID system, for instance, can drastically improve inventory tracking. which can help minimise losses, delays, and even theft. Meanwhile, installing automated conveyor systems can speed up product transportation within the warehouse and reduce manual labour.
Artificial intelligence (AI) and predictive analytics also hold great promise for improving warehouse management. With AI’s ability to analyse large amounts of data, you’ll be able to get more accurate demand forecasts based on past trends. AI can also be used to automate repetitive tasks such as reordering, allowing your workers to focus on more complex tasks.
6. Leverage Data Analytics for Continuous Improvement
Take advantage of data available to you to determine which areas are holding you back from improving your bottom line. This is possible by setting key performance indicators (KPIs) such as order accuracy, fulfillment speed, and inventory turnover to help you track warehouse efficiency. Having KPIs also lets you see which metrics are lagging behind over time.
Meanwhile, when choosing a WMS, make sure to pick one with a real-time dashboard that allows instant visibility into warehouse operations, which can empower you to make more proactive decisions. With the help of data-driven insights, you’re able to pinpoint inefficiencies and come up with strategic solutions, therefore enhancing overall warehouse performance.
To keep up with customer demands, reduce operational costs, and maximise revenue, warehouses are expected to improve themselves further through wise investments and strategic decision-making. Let the strategies above be your starting point in improving your warehouse’s bottom line to ensure long-term sustainability and profitability.